Shoes. Something I’ve been meaning to try for mumblty years so here goes. I’ve studied the book “Leather and Leatherworking in Anglo-Scandinavian and Medieval York” by Quita Mould, Ian Carlisle, and Esther Cameron ever since I found it in York some 25 years ago. This is Volume 17 of the The Archaeology of York series and is a fabulous reference for making shoes, not only does it show you which types of shoes were found during which time periods, but it gives an idea of the pattern pieces used to create those shoes, the types of material and construction methods used to make them. I also have the Museum of London book “Shoes and Pattens” by Francis Drew and Margrethe de NeerGaard. For my time period, drawstring ankle boots were most common, but I wanted something more delicate looking, and so chose this style, several examples of which were found in Perth Scotland:
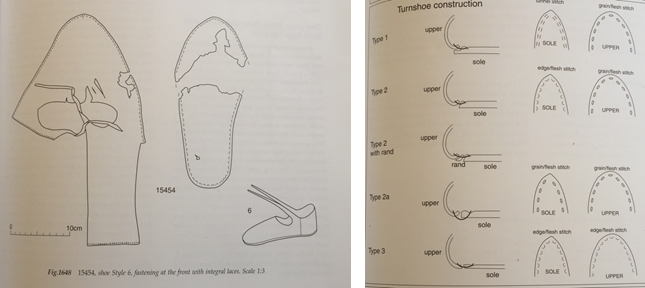
In Scotland, in the 12C, leather for the sole and upper came predominantly from cow or calfskin that was vegetable (oak) tanned. The two parts were sewn together with a double running stitch using waxed thread of animal or vegetable fiber tipped with a pig’s bristle for the needle. The examples of the shoe found were either Type 2 or Type 3 meaning they were sewn with either a an edge/flesh:grain/flesh stitch, an grain/flesh:grain/flesh stitch, or an edge/flesh:edge flesh stitch (see figure 2 above). Starting in the early 12C, a rand was usually inserted in the seam between the sole and the upper to protect the stitching. A facing was often used to strengthen stressed areas such as lacing holes. Shoes in the 12C were commonly decorated with a “vamp stripe” which ran from the throat of the shoe to the toe as a series of inscribed and silk embroidered parallel lines as well as with top bands that were embroidered with cross stitching in silk and then whip stitched on.
The figures on the Chartres Cathedral don’t have much information to convey on period shoes, but there are plenty of extant examples as well as many images in manuscripts and stained glass from the 12C.
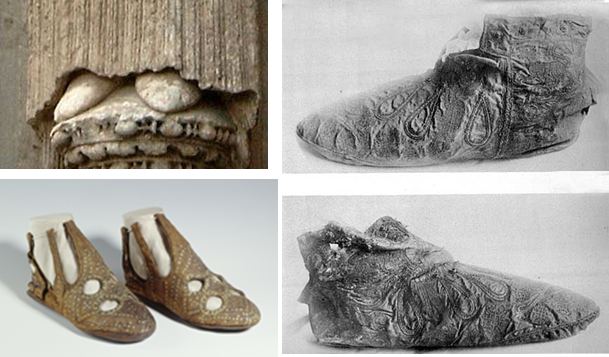
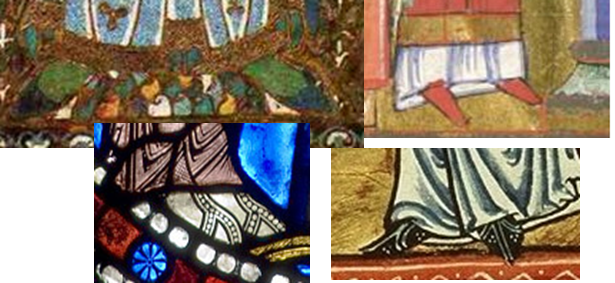
The first thing to do was to figure out a pattern. Now if you know me, you know I have a problem throwing out leftover materials once I finish a project. Well it just so happens I reupholstered some outdoor chairs last fall with some leather grained vinyl and had a small piece left over. It was a little heavier weight than the red leather, but had roughly the same flex and stretch. I made the sole by tracing my slipper sole, and the upper by shaping the vinyl over my foot, pinning the seam allowance to the area rug I was standing on, and then cutting a bit more so I could continue to shape it, and so on all around my foot. I then cut out the vinyl pattern, sewed it to the sole, and tried it on. It pinched at the top of the big toe and had extra floppy space to the side of the rest of the toes (I have very pointy feet) and the outside strap was too far toward the heel. So I marked up the pattern, cut it apart, and made a second pattern incorporating the changes. I sewed that one together and it fit perfectly, so I cut it apart to use as my pattern.
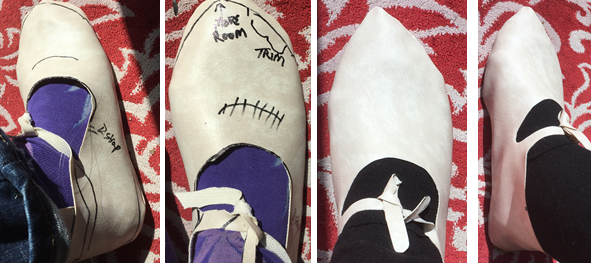
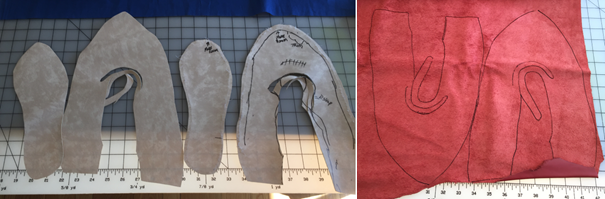
I have some lovely leather pieces picked up from a shoe repair shop that went out of business a few years ago, one of which is a very nice red calfskin. I chose to use this as the upper and some chrome tanned heavier leather for the sole. I cut out the pieces with my heavy garden shears and commenced sewing, and right away ran into problems. Sewing through the edge of the chrome tanned leather with the needle coming out through the flesh of the rite side of the sole and into the right side of the upper, the needle ripped the leather between where it entered on the side up through to the flesh where it exited, three stitches out of three. The chrome tanned leather is just too brittle to do this with. S I went back to my stash and found some caribou leather I had picked up at Birka several years ago. This leather was soft and pliable even though it was the same thickness as the chrome tanned leather. This leather allowed me to sew through the edge, out the flesh side, and into the upper with no problem, so away I went. I am sewing with an awl to poke holes, waxed sinew, a metal needle, a wooden drawer knob, and pliers. The wooden drawer knob with its big round top and the hole for the screw is so much better than a thimble! Something I learned many years ago at a Midrealm RUM class.
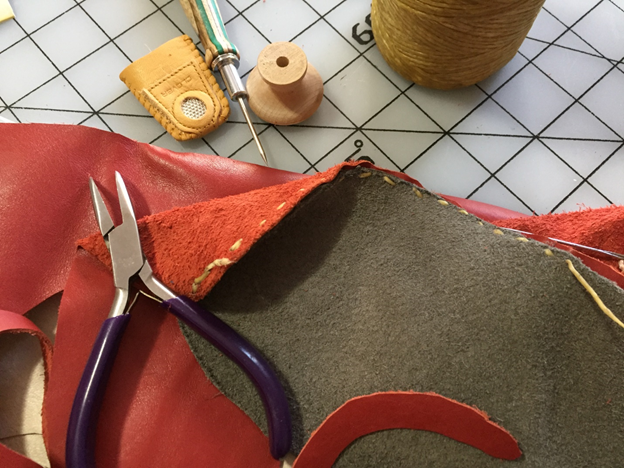